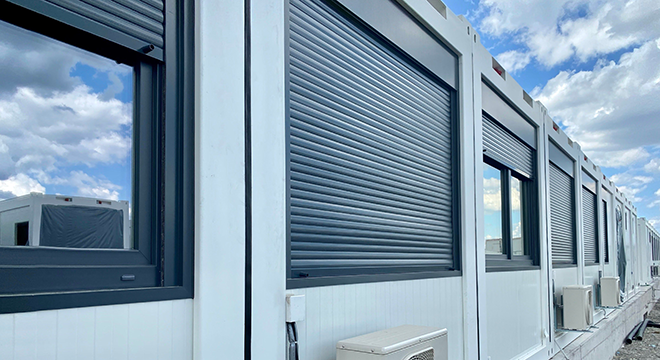
Dynamic economic conditions, and explosive growth in data center and semiconductor manufacturing and health care infrastructure demands, drive owners to explore and embrace modular building elements as they plan and execute today’s complex projects.
The mindset and perception that modular or prefab construction means quick, inexpensive cookie-cutter buildings is changing fast. In the U.S., traditional construction methods continue to get the job done, yet increasingly at a higher cost of time, materials and labor. The ability to adapt to market challenges such as longer lead times, supply chain issues and difficulty sourcing and retaining skilled labor is critical.
A recent Construction Dive article notes that convergence, or the blurring of lines between technology, process, manufacturing and architecture, is driving a construction industry renaissance as future-oriented firms rethink their approach.
We’ve outlined the top reasons industries are starting to embrace modular construction:
Faster Timeline
Research shows modular construction is 30 to 50 percent faster than traditional construction. Modular construction allows you to build off-site while doing site preparation simultaneously, ultimately shortening the completion timeframe for faster occupancy and ROI.
Cost-Efficient
Off-site modular construction typically results in more predictable schedules and fewer weather delays. A factory setting allows for processes, standardization and quality controls. When you combine that with volume purchasing and in-house testing, you can realize cost savings of up to 30 percent.
Increased Safety and Lower Risk
The biggest risk of injury on a job site is falling. Modular construction takes workers out of the field and places them in a more controlled factory environment. Working on the ground floor instead of several stories up significantly reduces the injuries caused by common job site dangers, like falling materials and ever-changing weather conditions. Reducing the risk of injury also reduces the impact on build timelines so projects stay on schedule.
Flexibility
Modular construction allows you to build as you grow versus having a massive building sit empty for future growth. It is also an ideal alternative for remote locations where an on-site building could prove difficult or expensive. Lastly, modular projects can be installed anywhere – on a roof, parking lot or adjacent to existing structures.
Scalability
The ability to add capacity — whether it be data center compute or additional mechanical support structures – reduces the risk of overbuilding and disruption at the job site. Modular buildings can optimize available or limited space with placement next to or on top of existing structures.
Protect Limited Resources
Modular construction celebrates Earth Day year-round, reducing the amount of on-site waste, traffic, air pollution and excessive noise that comes with typical construction projects.
Learn and Leverage Advanced Technology
Implementing construction technology like BIM (Building Information Modeling), AR (Augmented Reality), VDC (Virtual Design and Construction), and DfMA (Design for Manufacturing and Assembly) will improve predictability and collaboration, making design, build, visualization and installation more cost-effective.
TDIndustries Partners with owners, architects, general contractors and vendors across industries to envision, design, execute and optimize modular products, services and solutions.
Still researching the options? Take this quick poll to share what interests you most.
More from the Blog
What's Driving Modular Data Center Growth?
It’s that time of year when the 2023 research, market data and trends are published, providing hope and...
How Modular Construction Benefits the Healthcare Industry
In December, CoStar published an article about construction backlog being at a three-year high. One of...
Five Reasons to Build a Career in Manufacturing
Finding a career that fits your skills, interests, schedule preferences and family responsibilities can...
Subscribe to our blog
Please provide your email address to subscribe!